The basic purpose of an oiling system is to provide lubrication for the engine. It doesn’t matter if the system is a wet sump with an internal oil pump mounted in the crankcase or front cover, or a dry sump system with an external multi-stage pump. The engine doesn’t know the difference as far as where the oil comes from – as long as the flow keeps coming at all RPMs and under all operating conditions.
Conventional wet sump oil systems are usually adequate for normal driving, and even many forms of racing as long as the ambient temperature, G-forces and engine RPMs are not too high. One of the weaknesses of wet sump systems is that they pull oil from the bottom of the oil pan. Keeping the oil where it belongs can be a major challenge in many types of racing.
When a drag car launches off the line, positive G-forces push the oil backwards. The oil wants to climb up the back of the engine and away from the oil pump pickup in the bottom of the pan. Then, when the car shuts down and decelerates at the top end of the strip, negative G-forces push the oil towards the front of the pan.
Most stock oil pans can’t control these kinds of forces, increasing the risk of oil starvation under hard acceleration or deceleration. That’s why many performance engine builds need an aftermarket oil pan with additional oil capacity, internal baffles and/or trap doors to control oil sloshing inside the pan. The oiling system should be a high priority rather than an afterthought to protect the engine.
With circle track applications, sideways G-forces are constantly pulling the oil towards the right side of the pan because the car is always turning left. The oil pan for a circle track car also needs additional oil control baffles, an extended side cavity or kickout on the right side and a relocated pickup so it can pull in oil from the right rear corner of the pan.
Road racecars face an even tougher challenge. In addition to extreme fore and aft G-forces generated by accelerating and braking, the oil in the crankcase experiences sideways G-forces in both directions. This calls for even better baffling, trap doors and kickouts to keep the pump pickup submerged in oil.
A well designed oil pan should allow oil to return to the pan as quickly as possible, direct oil that is flinging off the crankshaft back into the pan (directional scraper), minimize windage (drag and aeration) by shielding the oil in the pan from turbulence generated by the spinning crankshaft (which is worse with longer stroke cranks), and have the right kind of baffling and/or trap doors to keep as much oil as possible around the oil pump pickup inlet. A “budget” pan that fails to meet these criteria may end up costing you an engine.
With off-road vehicles and marine engines, a wet sump oiling system may have serious problems with oil control.
There can be negative vertical G-forces when the vehicle or boat goes airborne. These kinds of racing conditions can make it nearly impossible to keep oil in the sump. For these kinds of applications as well as many road race engines, a dry sump oiling system is often a better choice.
The last thing any racer wants to see when an engine is revving hard is a fluctuating or dropping oil pressure reading – or no oil pressure at all.
Bearings won’t survive very long once the oil film is lost. Coated bearings can provide some momentary protection if the oil film between the crank journals and bearings goes away, but not for long. So it’s important to have an oiling system that minimizes the risk of oil starvation.
Reserve Pressure
One solution to reducing the risk of oil starvation in wet sump systems is to install an oil pressure accumulator in the system. The accumulator functions as a pressurized oil reservoir. The accumulator builds up pressure when the engine is running, creating reserve emergency pressure for when it may be needed.
If the oil pump sucks air because extreme G-forces in any direction are pulling oil away from the pickup in the bottom of the pan, the accumulator reacts to the drop in pressure and provides the much-needed push to keep oil flowing to the motor.
Depending on the capacity of the accumulator, the reserve pressure might last for up to a minute or more. This can make the difference between winning a race and blowing a motor.
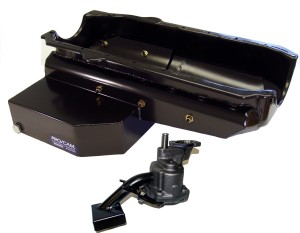
An accumulator can also provide additional oil flow and cooling for turbo motors after the engine has been shut down. This can prevent oil oxidation and coking on the turbo shaft bearings.
An accumulator can also be used to prelube the engine prior to starting it up. Various types of manual and electric solenoid valves are available for accumulators.
The manual variety has to be opened prior to starting the engine, and closed before shutting it off. Solenoid valves can be switched on and off remotely, or controlled by an oil pressure sensor at opens at a preset pressure. Either way, having a shot of reserve oil pressure ready to pressurize the engine can minimize the risks of dry starts and oil starvation.
An accumulator can also compensate for any loss of oil pressure that results from oil pump cavitation. When many spur gear oil pumps reach 5500 to 6000 RPM, the gears may be spinning faster than oil can flow into the pump. This creates tiny bubbles in the wake of each gear tooth that aerates the oil and causes a drop in pressure.
The exact RPM at which cavitation occurs and how much pressure drop it causes depends on the design of the pump, the size, position and contours of the inlet port, the size of the pickup tube (larger is always better), the flow characteristics of the pickup inlet (less restrictive is always better) and oil viscosity.
A wet sump system with a relatively small pickup tube, restrictive drilled or screen mesh pickup inlet, a stock oil pump and a heavy viscosity motor oil (like straight SAE 50 or 20W-50 multi-viscosity racing oil) will cavitate and lose oil pressure at a much lower RPM than a system with a well-designed high flow oil pump, large pickup tube, minimally restrictive inlet and a lower viscosity oil (like 0W-30, 0W-40, 5W-20, 5W-30 or 10W-30 synthetic racing oil).
Which Oil Pump Is Best?
Many replacement oil pumps designed for performance use have thicker, stronger castings, or CNC machined billet housings to reduce the risk of breakage. Close internal tolerances are essential to minimize internal pressure losses and to maximize the pump’s output.
Many performance oil pumps also offer increased flow and/or pressure. Taller gears and larger ports increase flow while a stiffer or adjustable bypass spring increases pressure. A high volume pump is recommended for engines with looser bearing clearances. A high volume pump can also be used to maintain “normal” oil pressure readings with lower viscosity synthetic motor oils. But a high volume oil pump should not be used as a bandaid to make up for sloppy bearing clearances inside an engine.
For an engine that will seldom rev beyond 6000 RPM, a stock flow pump may be all that’s needed to keep the engine lubed.
For higher RPMs, a high volume pump can increase flow 15 to 20 percent or more over a stock pump. But to get maximum flow out of a high volume oil pump, you should also install the largest possible pickup tube that will fit the application – and make sure the inlet is as nonrestrictive as possible. The inlet also must be positioned at the right height so it doesn’t restrict flow or suck air.
Most pickup tube inlets should be positioned about 1/4 to 3/8 inch above the bottom of the pan. If the position of the inlet is too high, it increases the risk of oil starvation when high G-forces are present. If the inlet is mounted too close to the bottom of the pan, there may not be enough clearance for good oil flow at higher RPMs.
If you don’t know how much clearance is actually between the pickup tube inlet and bottom of the pan, put a small ball of modeling clay in the bottom of the pan, install the pan temporarily, then remove the pan and measure the thickness of the clay once it has been deformed by the inlet.
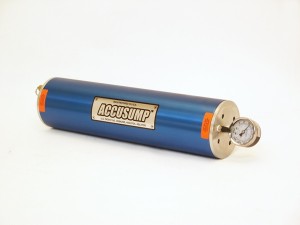
And make sure you don’t leave any clay in the pan or pickup tube inlet!
The least restrictive type of oil pickup inlet is one that is covered by a large open honeycomb mesh or coarse screen. Inlets that have a welded metal box on the end with drilled holes can be restrictive if the holes are too small or there are not enough holes to allow good oil flow at higher RPMs.
The only thing the inlet screen or mesh does is prevent big chunks of debris from being pulled into the pump if the engine blows a bearing, piston or a rod. It provides no real filtration or wear protection for the oil pump.
A restrictive pickup tube inlet can also make it harder for an oil pump to self-prime when a cold engine is first started. Cold oil, especially a heavy viscosity oil like straight 40 or 50 weight racing oil, flows like molasses until it gets hot. This can delay the time it takes for oil pressure to build inside the engine and for the oil to reach the upper valve train components.
Multi-viscosity racing oils, by comparison, are much thinner when cold, which makes it easier for the oil pump to pull oil up through the pickup tube. A thinner viscosity oil will build pressure faster and lubricate upper valve train components much quicker.
Some racers are leery of multi-viscosity oils, thinking they are too thin to provide adequate lubrication protection. However, once the oil gets hot, it acts the same as heavier viscosity oil. A 20W-50 racing oil, for example, will flow like a 20 weight oil when cold, but cling to the bearings like a 50 weight oil when its hot.
How Much Oil Pressure Do You Really Need?
For many years, engine builders and racers liked to see at least 10 PSI of oil pressure for every 1000 RPM of engine speed. Some guys are not happy unless their oil pressure gauge is reading 60 PSI at idle! Truth is, most engines don’t need that much oil pressure.
Oil pressure is resistance to flow, and it robs horsepower. Consequently, if you provide enough oil flow to keep a steady oil film in the bearings but no more, you can save some horsepower that would otherwise be wasted spinning the oil pump.
Many performance engines can get along just fine with only 4 to 5 PSI of oil pressure for every 1000 RPM – provided the crankcase is filled with a high quality oil that can maintain good film strength and contains enough anti-wear additive.
Oil pressure is also a direct function of bearing clearances. If you build an engine with standard bearing clearances and then fill the crankcase with a low viscosity synthetic oil (like 0W-30 or 5W-20), you will see a corresponding drop in oil pressure.
Why? Because the oil is thinner and flows through the bearings quicker than a heavier oil such as a 20W-50 or straight 30, 40 or 50 weight oil. Consequently, you can tighten up the bearing clearances a bit and take advantage of the thinner viscosity oil to gain some horsepower.
Or, you can stick with the way you’ve always built engines, leave the bearings with standard or slightly loose clearances and go with a traditional 20W-50 racing oil or a heavy straight weight oil.
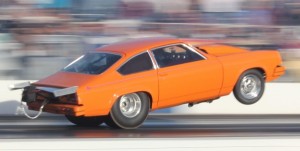
Dry Sump Oil Systems
For racers who have experienced oil starvation problems or engine failures from loss of oil pressure, a dry sump oiling system is usually the recommended cure.
Yes, dry sump oil systems are expensive, costing up to several thousand dollars for a basic 3-stage setup (and even more for multi-stage systems), but you get what you pay for.
A dry sump oil system uses a series of suction pumps to pull oil vapor out of the crankcase. Additional hoses and scavenge pumps can also be used in a multi-stage setup to pull air and oil out of the lifter valley and valve covers. Pulling air and oil vapor out of the engine reduces windage inside the crankcase and saves horsepower. It also allows the use of a very shallow oil pan because the pan doesn’t have to hold any liquid oil or function as a sump.
A shallow oil pan provides more ground clearance under the engine and/or allows the engine to be mounted lower in the chassis to lower the center of gravity.
The oil vapor siphoned out of the crankcase by the suction pumps is routed to an externally mounted separator/reservoir tank.
The tank separates the air from the oil and collects the liquid oil so it can be fed to an externally-mounted gear or belt driven oil pump. The tank provides a constant supply of oil so the pump never runs dry. The additional oil capacity provided by the tank also helps keep oil temperatures lower.
The amount of oil held by the tank may range from as little as 6 to 8 quarts for a turbocharged four-cylinder engine to 8 to 12 quarts for a typical V8.
For a marine application, tanks that hold 5 to 6 gallons of oil are commonly used to compensate for all the pounding and sloshing that occurs in this type of racing. Some off-road racers and rock climbers have even mounted oil tanks with a gimbal arrangement to keep the tanks vertical as the vehicle tilts fore and aft or side-to-side.
With long stroke crankshafts, there can be a lot of windage and drag inside the engine. By using a multi-stage dry sump system with additional suction pumps, it’s possible to create and maintain vacuum inside the crankcase to reduce windage drag on the crank – especially at higher RPMs. The higher the vacuum, the less drag. Vacuum in the crankcase also helps ring sealing.
A two-stage or three-stage dry sump oil system with two or three scavenge pumps stacked together will usually not pull enough suction to create high vacuum inside the crankcase.
But a four-stage, five-stage or six-stage dry sump oil system that is sucking air and oil out of the crankcase and lifter valley can generate high levels of vacuum, even at high engine speeds and loads when blowby increases. The hot setup these days is a six-stage system that uses one suction pump to pull air and oil out from under each pair of cylinders on a V8, plus two more pumps to suck vapors out of both ends of the lifter valley under the intake manifold.
Engines equipped with a dry sump oiling system have to be sealed so they don’t pull in outside air. That means no open valve cover, lifter valley or crankcase vents.
Depending on the level of vacuum you want to achieve, you may have to install crankcase end seals with reversed lips to prevent air from being pulled past the seals.
As with wet sump oiling systems, you only need to feed the engine with as much oil flow as it actually needs.
Flooding it with oil pressure only wastes horsepower. You want to maintain minimum oil pressure and flow without over-oiling the engine.